Technology Innovation Institute Unveils AMALLOY-HT, First Metal Additive Manufacturing Alloy Designed in Middle East for Harsh Operating Conditions
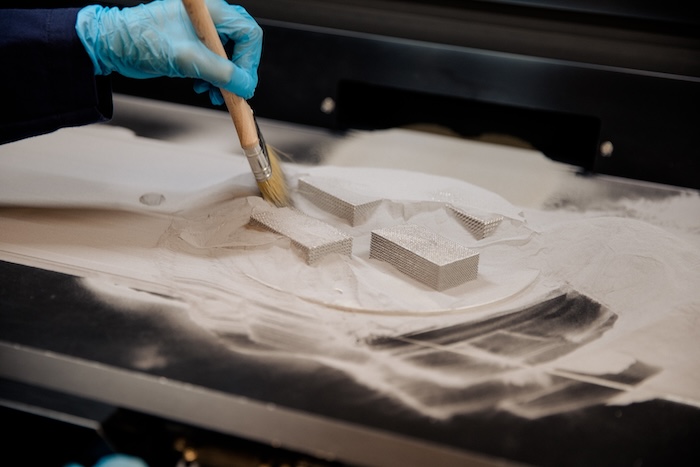
The Technology Innovation Institute (TII), a leading global scientific research center and the applied research pillar of Abu Dhabi’s Advanced Technology Research Council (ATRC), is making headlines with the latest addition to its groundbreaking portfolio of additive manufacturing materials – AMALLOY-HT. The proprietary new aluminium alloy powder is the first metal additive manufacturing feedstock designed in the Middle East for use in Powder Bed Fusion – Laser Beam (PBF-LB) systems.
A breakthrough innovation from TII’s Advanced Materials Research Center (AMRC), AMALLOY-HT successfully solves long-standing issues faced by the metal additive manufacturing industry pertaining to the use of the Powder Bed Fusion – Laser Beam (PBF-LB) technique. The approach, which utilizes a high-energy source to melt the raw material and shape it as needed, has found uptake within various industry use cases. However, challenges persist given the aggressive nature of the laser-material interaction involved in the process that causes cracks and other manufacturing defects in a range of materials, specifically the high-strength ones.
Thanks to TII’s research and development, the palette of high-strength metals that are 3D-printable is now expanding. AMALLOY is the first low-cost, high-strength aluminium alloy wholly designed and produced by a team of researchers in the UAE. The AMALLOY family of materials boasts remarkable strength and an incredibly low hot crack susceptibility coefficient.
Not long after announcing the launch of AMALLOY, the newly released, high-temperature variant of the alloy ‘AMALLOY-HT’ demonstrates excellent thermal stability, especially in extremely high-temperature environments (up to 300°C). It is worth noting that 300 degree Celsius is the maximum operating condition for any aluminium alloy as aluminium degrades beyond this temperature.
The material’s versatility and high-temperature resistance will unlock exciting possibilities in myriad sectors, ranging from automotive, aviation, aerospace engineering, and space exploration to oil and gas and energy. Among its use cases, AMALLOY-HT can be used to manufacture pistons in racing cars and satellites.
Speaking on this exciting development, Dr. Nesma Aboulkhair, Director of Additive Manufacturing at TII, said: “While there have been several examples of new materials for additive manufacturing emerging from laboratories in the US, Europe, and Australia, this is the first time the UAE has joined the elite list of countries with sovereign capabilities in this domain. We are now cultivating the expertise to produce metal powder and design innovative materials, empowering us to manufacture existing alloys and create new ones for both local and global markets.”
The introduction of AMALLOY and its new high temperature variant are set to boost international collaboration opportunities for researchers, manufacturers, and industry leaders, and allow them to harness the full potential of these advanced materials across domains. TII has already filed two patents with the U.S. Patent and Trademark Office for AMALLOY and AMALLOY-HT and plans to use its framework to develop alloys from other metal families.
Dr. Federico Bosio, Lead Researcher in Additive Manufacturing Materials at TII, said: “As part of TII’s ongoing commitment to innovation, AMALLOY-HT will continue to undergo refinement, fine-tuning, and even more comprehensive testing. The goal is to commercialize the high-strength aluminium alloy specifically designed for high-temperature applications. While this material creates a plethora of new opportunities and solutions for industries around the world, it will also elevate Abu Dhabi and the UAE’s reputation as a hub for cutting-edge research and development.”